Injection molding is a pivotal process in the manufacturing industry, known for its ability to produce complex plastic parts with high precision and repeatability. This blog will provide a comprehensive overview of injection molding, including its history, process, and significance to manufacturers.
The History of Injection Molding
Early Beginnings
The history of injection molding dates back to 1872 when John Wesley Hyatt and his brother Isaiah developed the first injection molding machine. This early device was relatively simple, using a plunger to inject plastic into a mold. The initial applications were limited to producing basic items like buttons and combs.
In the Mid-20th Century
The real breakthrough in injection molding came in the mid-20th century with the invention of the screw injection molding machine by James Watson Hendry in 1946. This innovation allowed for better control over the injection process, leading to higher quality products and the ability to use a wider range of plastic materials.
Modern Injection Molding
Today, injection molding technology has advanced significantly. Modern machines are capable of producing extremely complex parts with tight tolerances. The use of computer-aided design (CAD) and computer-aided manufacturing (CAM) has further enhanced the precision and efficiency of the injection molding process.
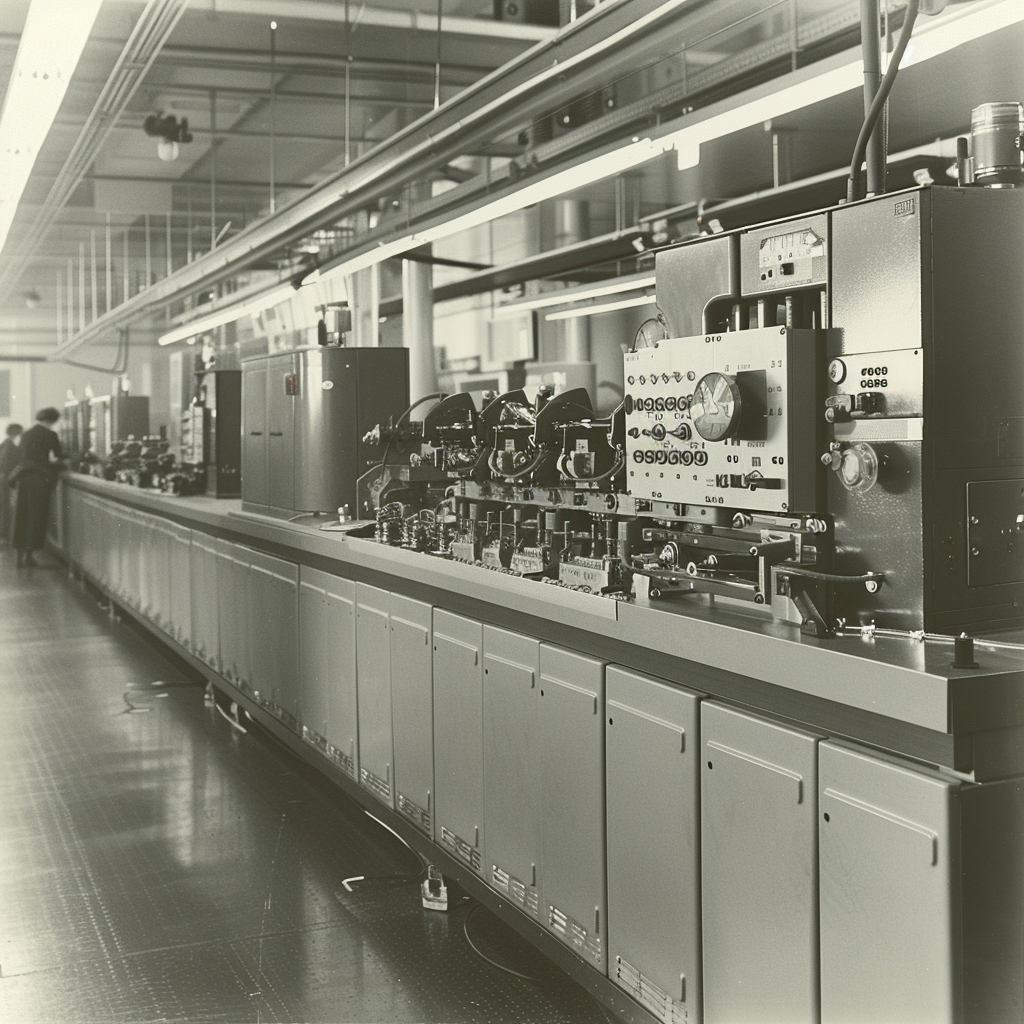
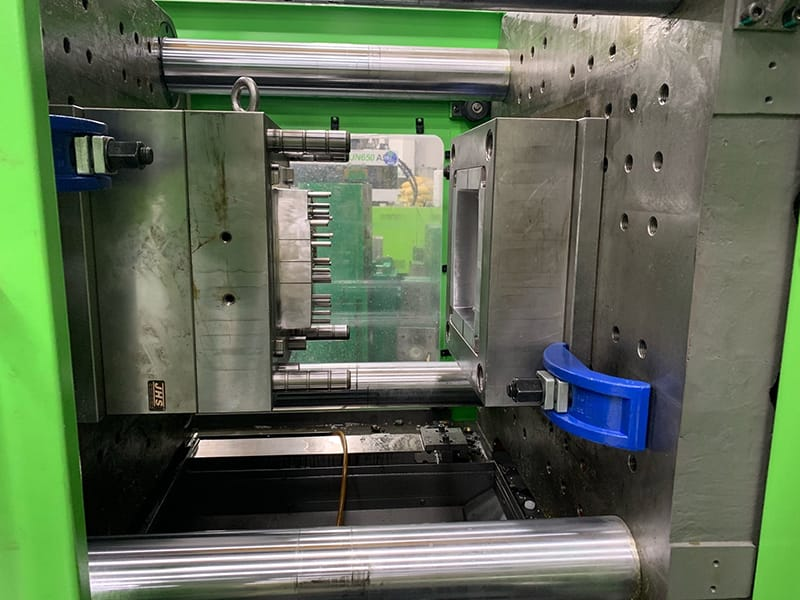
Clamping: The mold is clamped shut under high pressure.
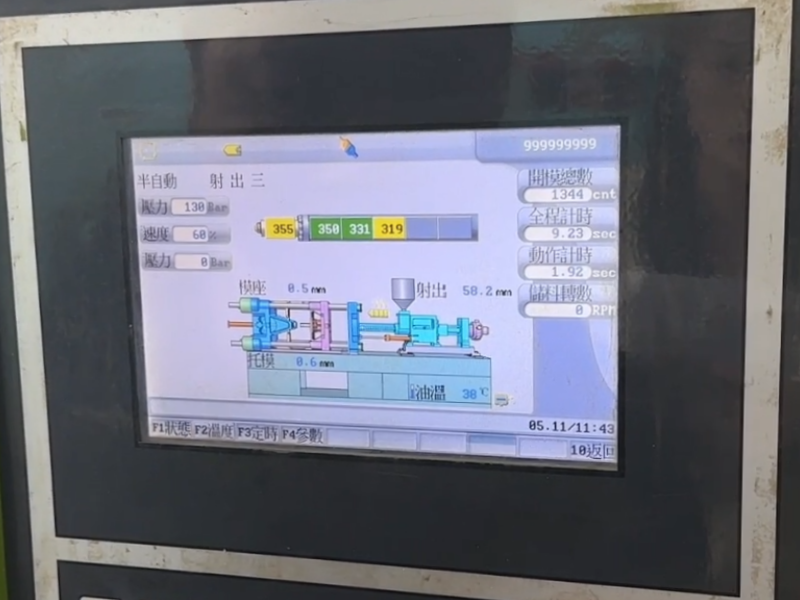
Injection: Molten plastic is injected into the mold cavity.
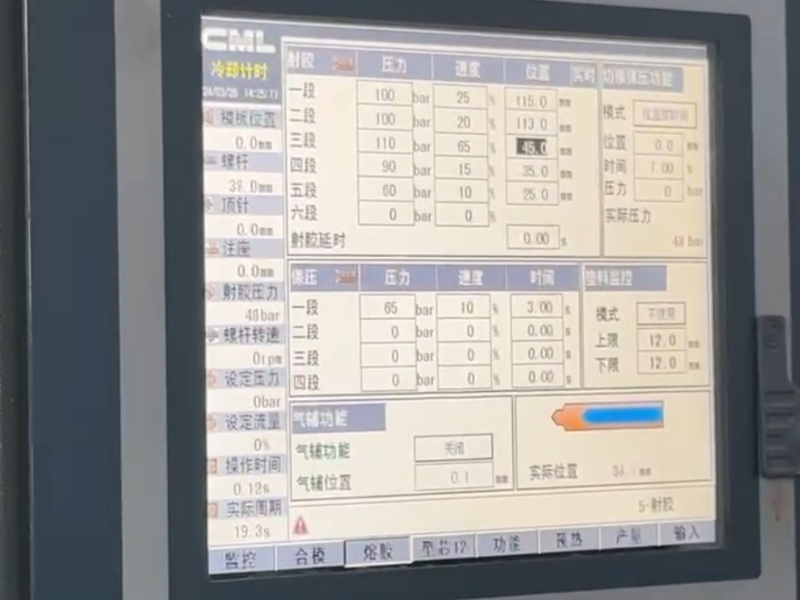
Cooling: The plastic cools and solidifies within the mold.
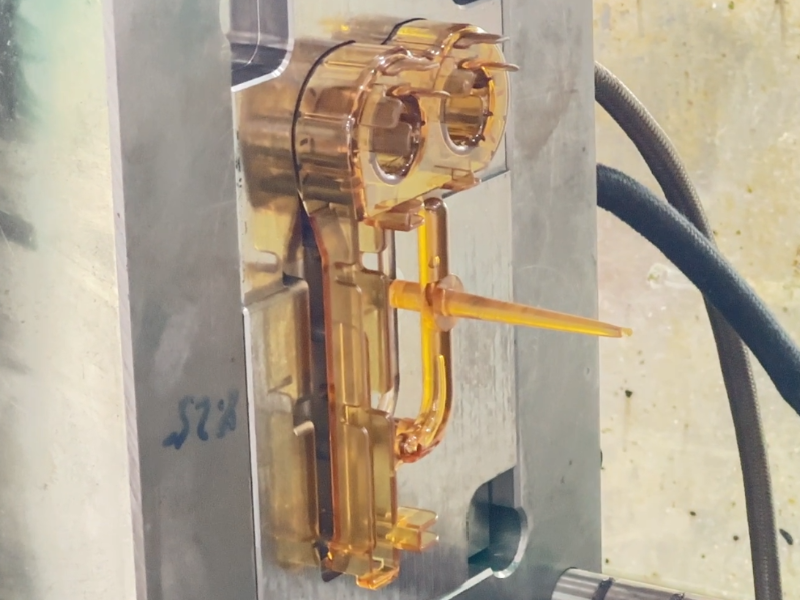
Ejection: The finished part is ejected from the mold.
Each of these steps must be precisely controlled to ensure the quality of the final product. The ability to automate and fine-tune these parameters makes injection molding highly efficient and suitable for mass production.
Importance of Injection Molding to Manufacturers
High Efficiency and Repeatability
One of the main advantages of injection molding is its ability to produce large volumes of identical parts quickly and efficiently. This is crucial for industries that require consistent quality and high production rates, such as automotive, medical, and consumer electronics.
Material Versatility
Injection molding can handle a wide variety of materials, including thermoplastics, thermosetting plastics, and elastomers. This versatility allows manufacturers to choose the best material for their specific application, balancing factors like strength, flexibility, and cost.
Cost-Effectiveness
Although the initial cost of designing and creating molds can be high, the per-unit cost of injection-molded parts is relatively low. This makes injection molding a cost-effective solution for large-scale production runs.
Complex Geometries
The process can produce parts with intricate designs that would be difficult or impossible to achieve with other manufacturing methods. This capability is essential for creating complex components used in high-tech and precision industries.
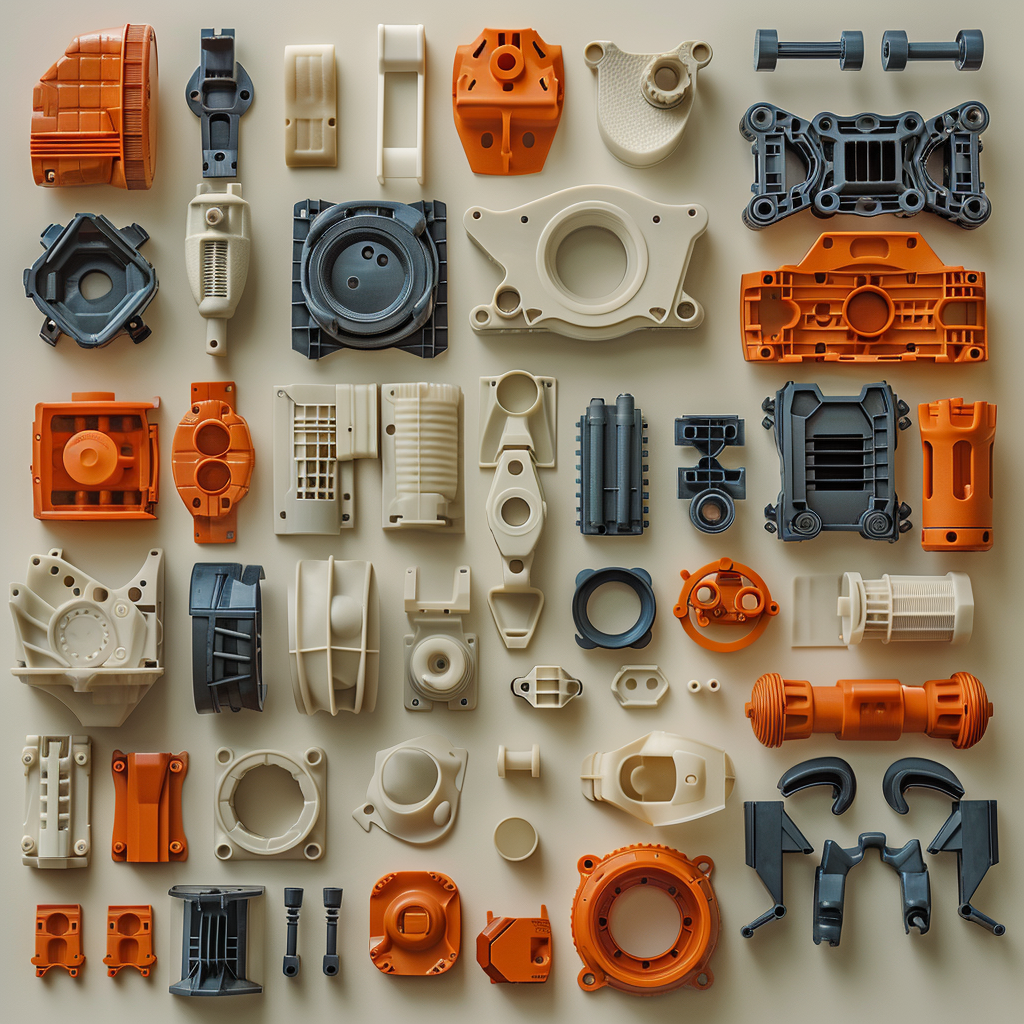
Conclusion
Injection molding is a cornerstone of modern manufacturing, offering unmatched efficiency, versatility, and precision. Its ability to produce complex parts in large quantities makes it invaluable to numerous industries. As technology continues to advance, the injection molding process will undoubtedly become even more integral to the production of high-quality plastic parts.