Custom Plastic Products Services
Classic Custom Products
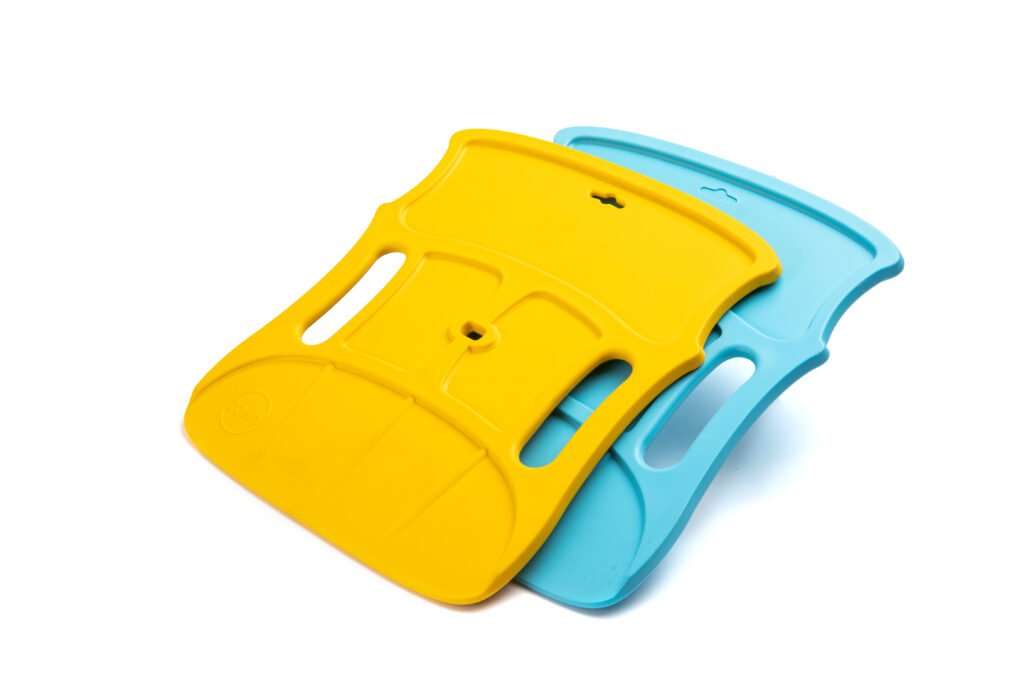
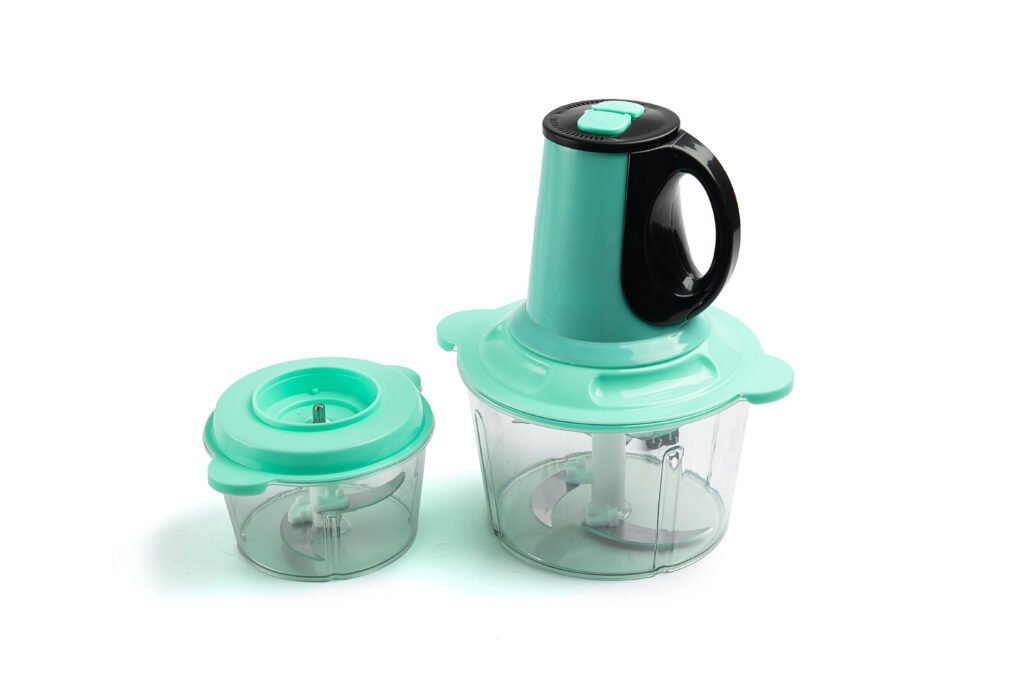
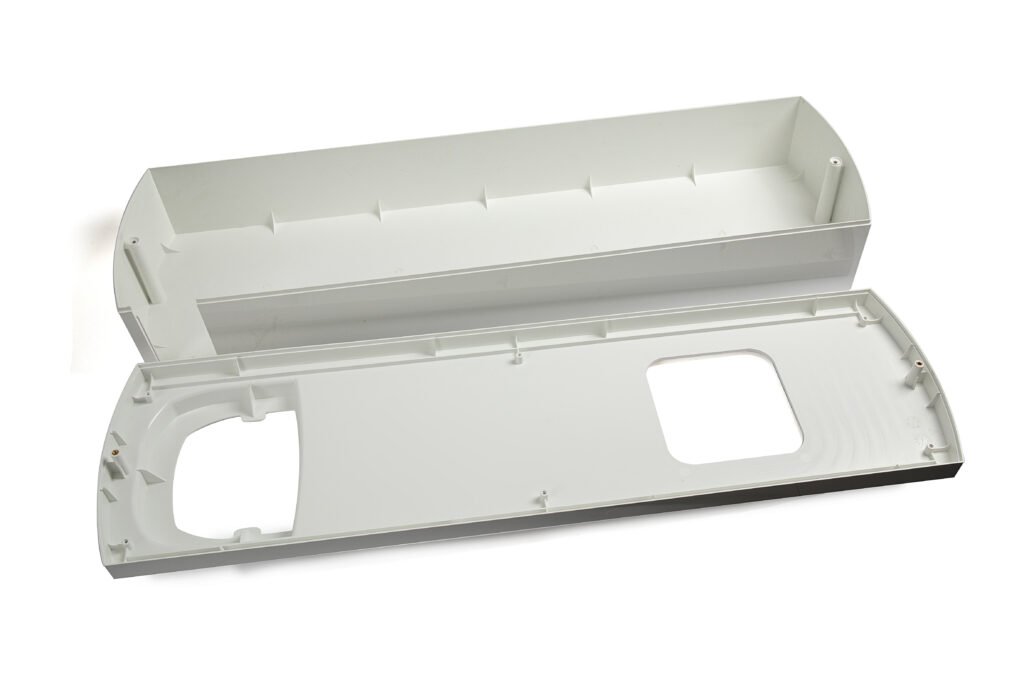
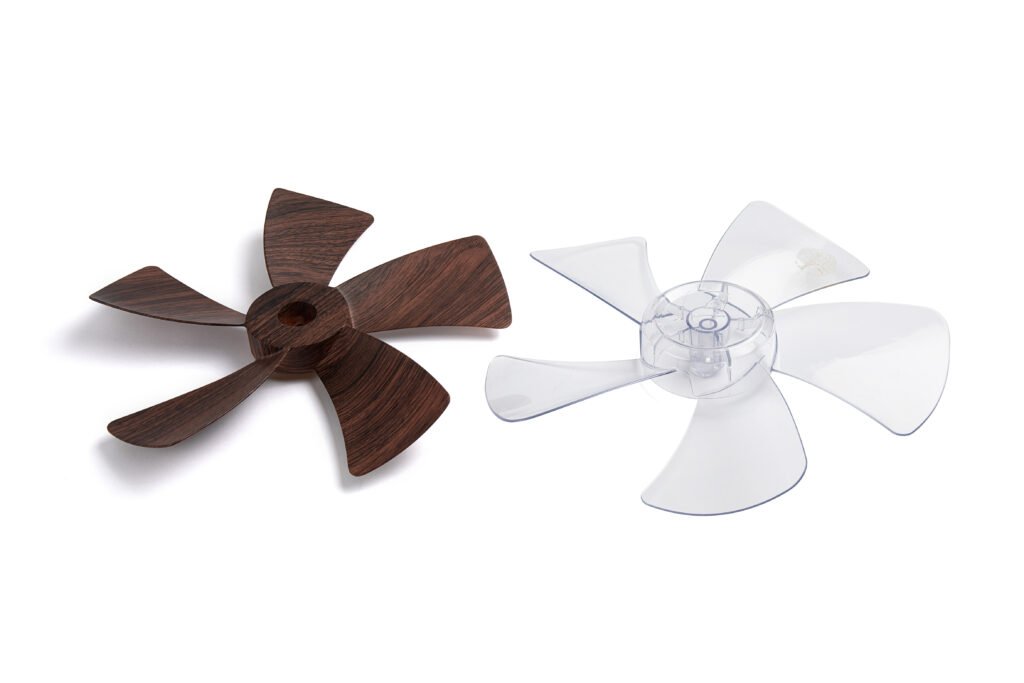
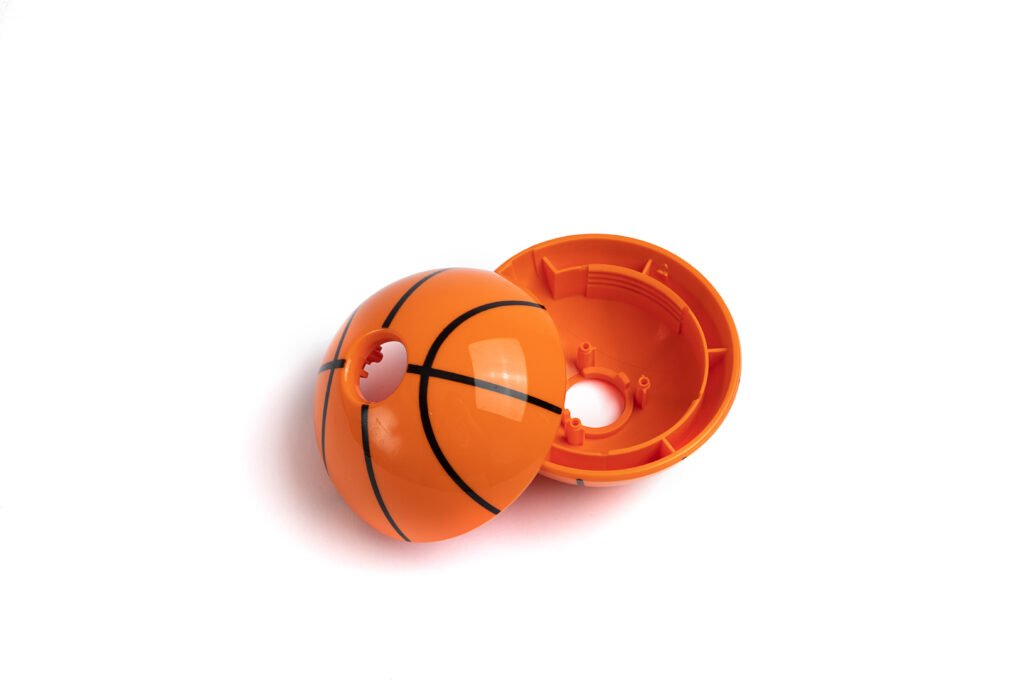
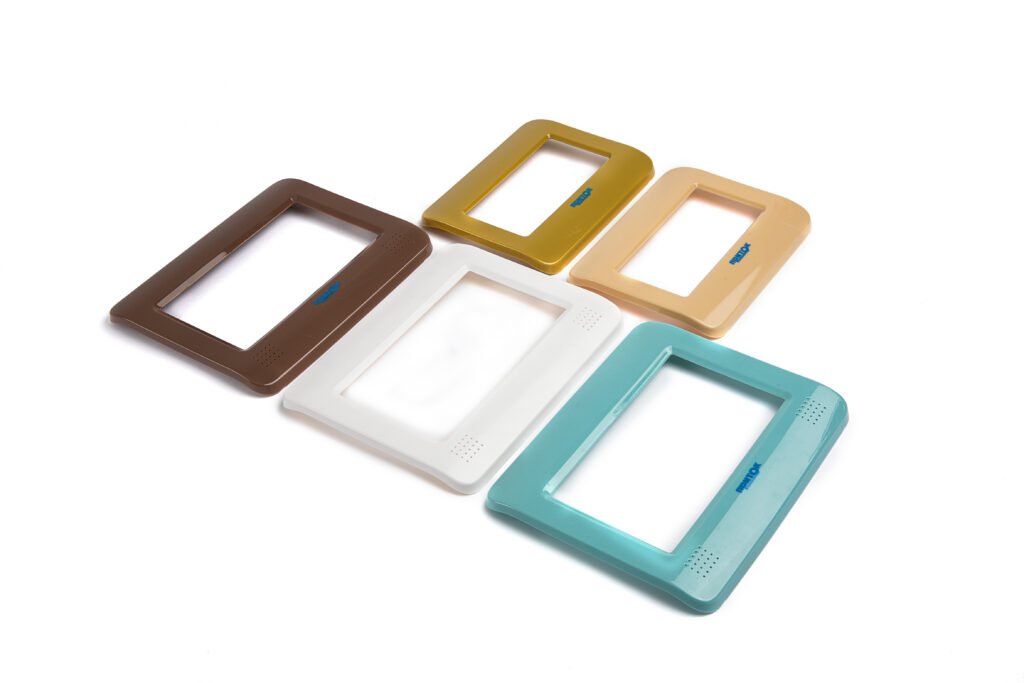
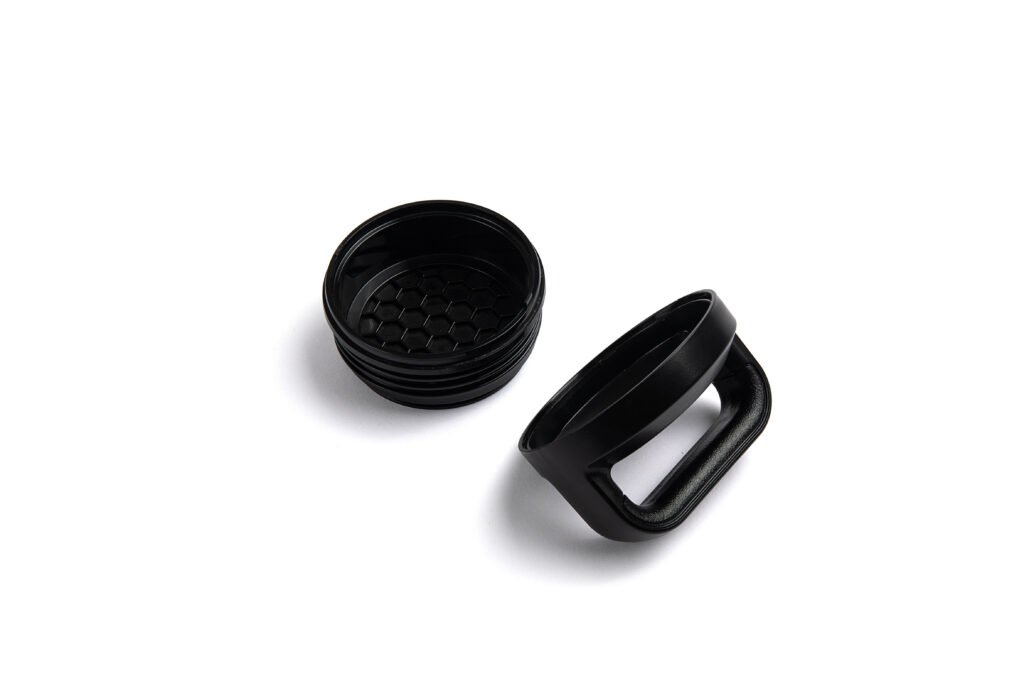
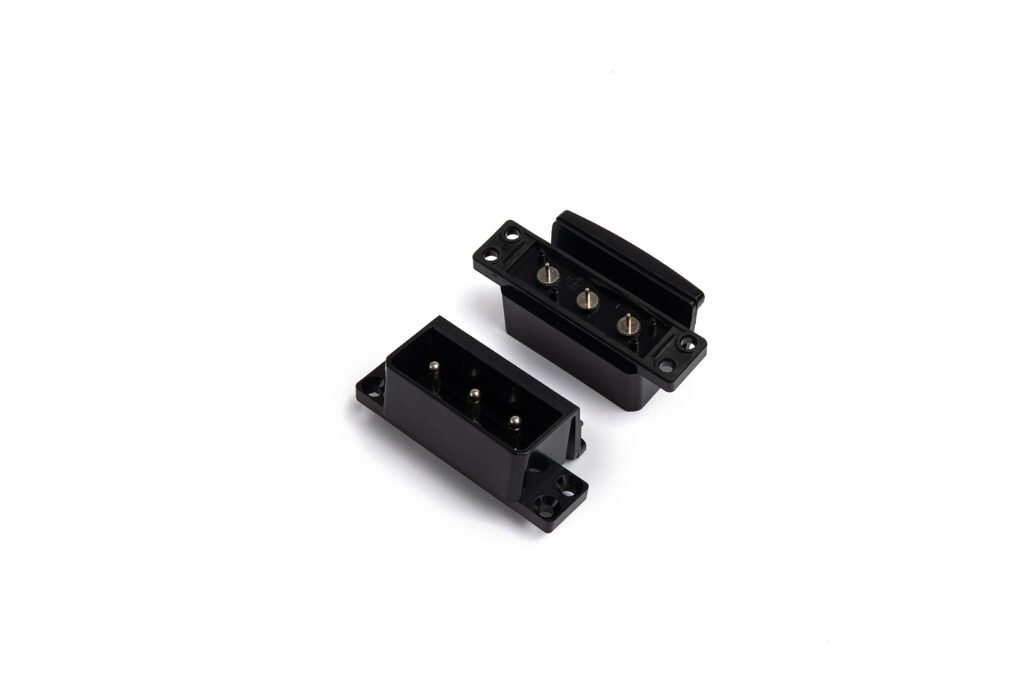
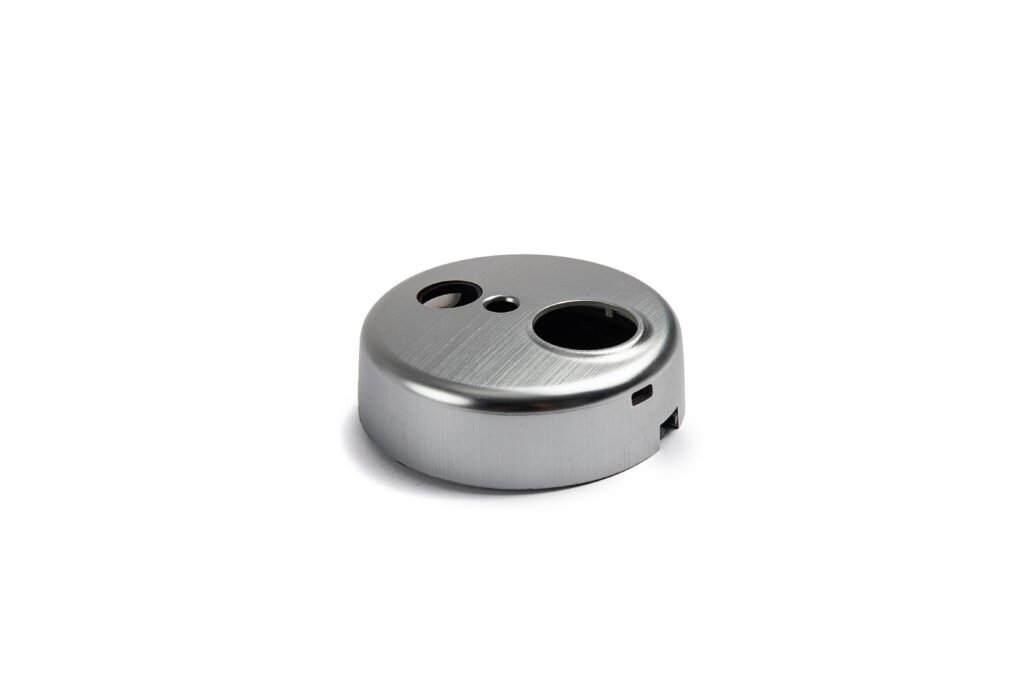
REQUEST A QUOTE FOR MORE DETAILS
Top Advantages of Injection Molding Solutions
High Production Efficiency
Injection molding is a highly automated manufacturing method that enables rapid mass production of parts. This efficiency makes injection molding ideal for large-scale manufacturing, reducing production costs.
High Precision and Consistency
Injection molding enables high-precision part production, ensuring consistency across batches. This is especially beneficial for industries that require high accuracy, such as automotive and electronics.
Material Versatility
Injection molding is compatible with a wide variety of plastic materials, including thermoplastics, thermosets, and elastomers. Different materials can be chosen to achieve the desired performance based on specific application needs.
Reduced Waste
Injection molding produces minimal waste, and excess material can often be recycled. This reduces material waste and is more environmentally friendly.
Design Flexibility
Injection molding supports complex geometric designs, allowing manufacturers to produce parts with a wide range of shapes and intricate details. This flexibility helps meet specific requirements across different applications.
Enhanced Part Strength
By controlling material and process parameters, injection molding can produce parts with excellent strength and durability, making it suitable for applications requiring high resilience and durability.
Inside the Injection Molding Process
Industries and Applications Best Suited for Injection Molding
Factors to Consider in Injection Molding
1.Material Selection
2.Mold Design
3.Cooling System
4.Injection Speed and Pressure
5.Cycle Time
6.Quality Control
Wanna dig deeper in custom plastic parts?
The mold and its Production Process
Please note that the final cost depends on the customized service you require, the specifications of the raw materials used, the relevant national laws, and the distance of transportation. Take the example of booking a tall container of products:
Step 1: PROJECT ANALYSIS & MOULD DESIGN (3-7 days)
At Ruicheng, we start by thoroughly analyzing your project requirements and then proceed to design the mould. Our experienced engineering team uses advanced CAD software to create precise mould designs that ensure high quality and efficiency, tailored specifically to your project’s needs.
Step 2: MOULD MATERIAL PREPARATION (within 1 day)
At Ruicheng, selecting the right mould material is crucial to ensure durability and performance. We begin by understanding the specific requirements of your project, including the type of plastic, production volume, and operating conditions. Our experts then recommend the most suitable mould materials, such as high-grade steel or aluminum, to match your needs. This careful selection process ensures that the moulds we produce are robust, wear-resistant, and capable of delivering high-quality parts consistently.
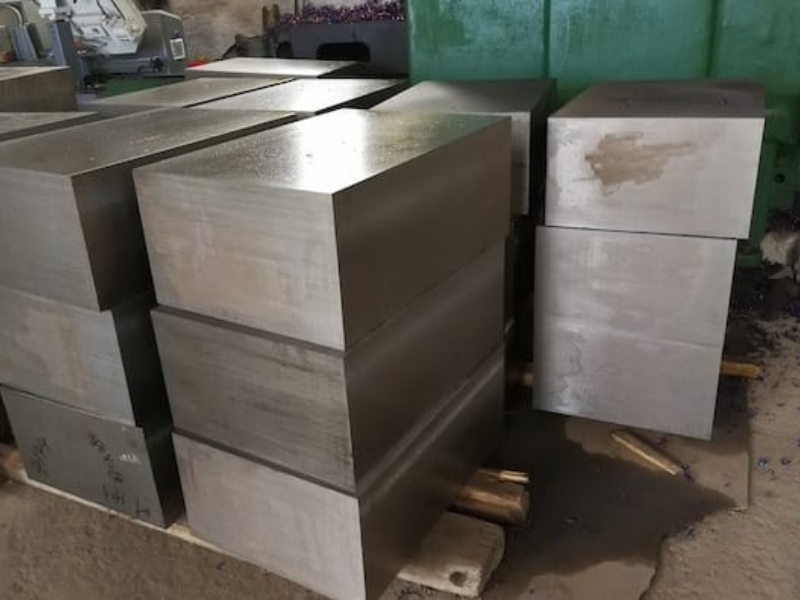
Step 3: MOLD PROCESSING (15-25 days)
At Ruicheng, mold processing is a critical step in ensuring product quality and performance. Our process begins with high-precision CNC machining, which accurately cuts mold materials to the required shapes and dimensions. We then utilize Electrical Discharge Machining (EDM) technology to handle intricate mold details, ensuring precision in every small part. To enhance mold durability, we perform heat treatment and surface treatment, improving the mold’s hardness and corrosion resistance. Finally, we conduct rigorous quality inspections to ensure each mold meets the highest quality standards, providing our clients with the best production solutions.
Step 4: MOULD TRIAL (1-3 days)
The mould trial phase is crucial for validating the mould’s performance and ensuring it meets all project specifications. During this stage, we conduct a series of test runs using the mould to produce sample parts, specifically using black material for T0 samples, as black material most easily reveals any issues. Our team meticulously examines these samples for dimensional accuracy, surface finish, and overall quality. Any necessary adjustments are made to optimize the mould’s performance. This thorough trial process ensures that the mould will produce consistent, high-quality parts in full-scale production, showcasing our commitment to professional and reliable manufacturing solutions.
Step 5: INJECTION PRODUCTION (5-10 days)
In the injection production phase, we transition from testing to full-scale manufacturing. Using advanced injection molding machines, we produce high-quality plastic parts with precision and efficiency. Our automated processes ensure consistent product quality and optimal production speed. Throughout production, we maintain stringent quality control measures, inspecting parts for any defects and ensuring they meet all specifications. This phase is where our expertise and technology come together to deliver reliable and high-performance plastic products to our clients.
Step 6: PRODCUTS INSPECTION (within 1 day)
In the products inspection phase, we ensure that every produced part meets the highest quality standards. Our inspection process includes rigorous checks for dimensional accuracy, surface finish, and mechanical performance. Using advanced inspection equipment and technologies, such as optical inspection systems and mechanical testing machines, we can identify and correct any potential defects. Through detailed quality reports, we guarantee that all products meet customer requirements and achieve the expected performance standards before final delivery.
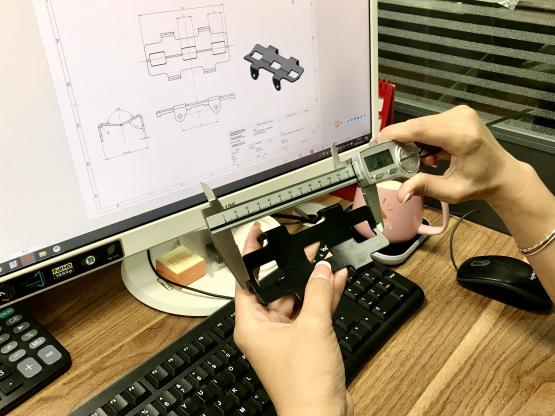
Step 7: Package (within 1 day)
In the packaging phase, we ensure that all products are securely packaged to protect them during transit and storage. Each item is carefully wrapped using appropriate protective materials such as bubble wrap, foam inserts, and corrugated boxes. Our packaging process is designed to prevent damage, preserve product integrity, and ensure that all items reach their destination in perfect condition. Clear labeling and detailed documentation are also included to facilitate easy identification and handling. Our commitment to quality extends to every aspect of the process, including packaging, ensuring complete customer satisfaction.
If you place an order now, you will enjoy the following free services:
1, Free simple DFM report;
2, Free design improvement suggestions or modification;
3, Free VDI texture catalogue can be shipped by your courier account;
The Basic Knowledge About Injection Service
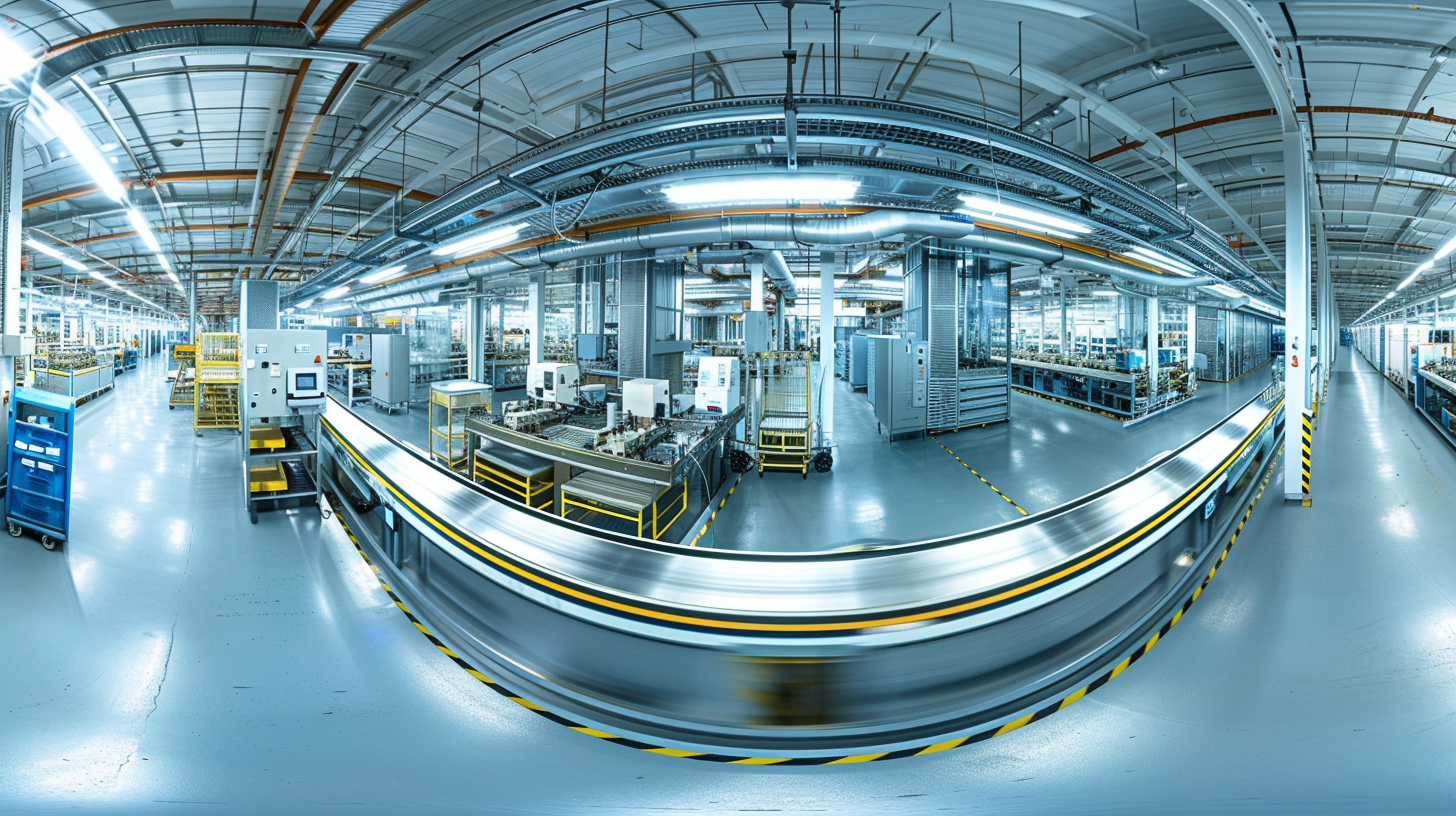
Our Advanced Equipment and Exceptional Material Processing Capabilities
At Ruicheng, we understand that eff
The FAQs About Our Injection Service
Find answers to the most frequently asked questions about our injection molding services. For further assistance, feel free to contact our team.
1.Can you make design drawings for me?
At Xiamen Ruicheng, we don't have in-house designers to create design drawings from scratch. However, our experienced engineers are fully capable of analyzing your existing designs. They can offer valuable design improvement suggestions and perform the necessary engineering work to ensure your project is optimized for production.
Feel free to share your designs with us, and we'll provide professional feedback and engineering support.
2.How long does a quotation take?
Once we receive your design files, our team will promptly review them. Typically, we can provide you with a detailed quote within 24hours, depending on the complexity of your design and any specific requirements you might have.
If you have a tight deadline, please let us know, and we'll do our best to expedite the process.
3.Can I use my own material for production?
Yes, it is OK to use your own material for production. At Xiamen Ruicheng, we are flexible and can accommodate customer-supplied materials. We will work with you to ensure that the material is suitable for the injection molding process and meets the requirements for your specific project.Just before starting the mould-making work, which material to be used for production is better to be decided. As different material its shrinkage rate is different that will result in different dimension finished product. The only concern is that yo have to undertake all the shipping price and import tariff of your material for us. We will suggest that you can send us the material its data sheet as our checking whether we can find the exact same in China or find a similar as a replacement to save the shipping price and tariff.
4.How do I know my design will be kept confidential?
At Xiamen Ruicheng, we understand the importance of confidentiality for your designs. To ensure your intellectual property is protected, before you are going to send us the design files, we can sign a NDA with you to make sure the design or following negotiation is confidential.
5.Why should I choose plastic injection molding(PIM)?
Not all projects are suitable for plastic injection molding. After having your project files to understand what it is and its quantity need, our engineer team will then offer you our recommendation accordingly.
6.How do you handle quality specifications?
By passing the ISO9001 quality system certificate, We have a full and strict quality control process from raw material until the final finished product for shipment. The finished product its inspection report can be offered from our inspection team before shipment. Or you can ask the third party inspection like SGS or others come and do the inspection.
7.Who own the injection moulds and How long you will keep the injection moulds?
You are the one who pays the moulds that have the ownership of the moulds. Xiamen Ruicheng can help you to keep the finished moulds safe in our warehouse for 3 years if there is not any production need during these 3 years. After 3 years, we will check with you whether the moulds are going to be used again, if not, we will have to break them to released our warehouse space and labor cost to maintain them.
If the moulds are used for production every year, we will keep them until they cannot be used any more to discuss with you whether it is time for making their new moulds to continue the production.
Get In Touch
Get in touch and let us know how we can help.
No.50, Liheng Industrial Zone, Xinglin West Road, Jimei District, Xiamen, China
marketing@chinaruicheng.com
WhatAPP : +8615159297535