What are Weld Lines?
Weld lines are linear defects formed during the injection molding process when molten plastic flows and rejoins in the mold. These lines typically appear at the intersections of plastic flow, such as where flow fronts collide, merge, or rejoin after bypassing obstacles. Weld lines not only affect the appearance of plastic parts but also reduce their mechanical performance and strength. For example, in high-stress applications, weld lines can become potential sources of cracks.
Effect of weld lines
Weld lines not only affect the appearance of products but also reduce their mechanical performance and structural integrity. Weld lines cause linear marks on the product surface, affecting its aesthetics, and can become potential sources of cracks and fatigue failure, reducing the strength and durability of the parts. Additionally, weld lines can impact the sealing and electrical performance of the products, increasing manufacturing costs and customer complaints. Therefore, addressing weld line issues is crucial to ensuring product quality and performance.
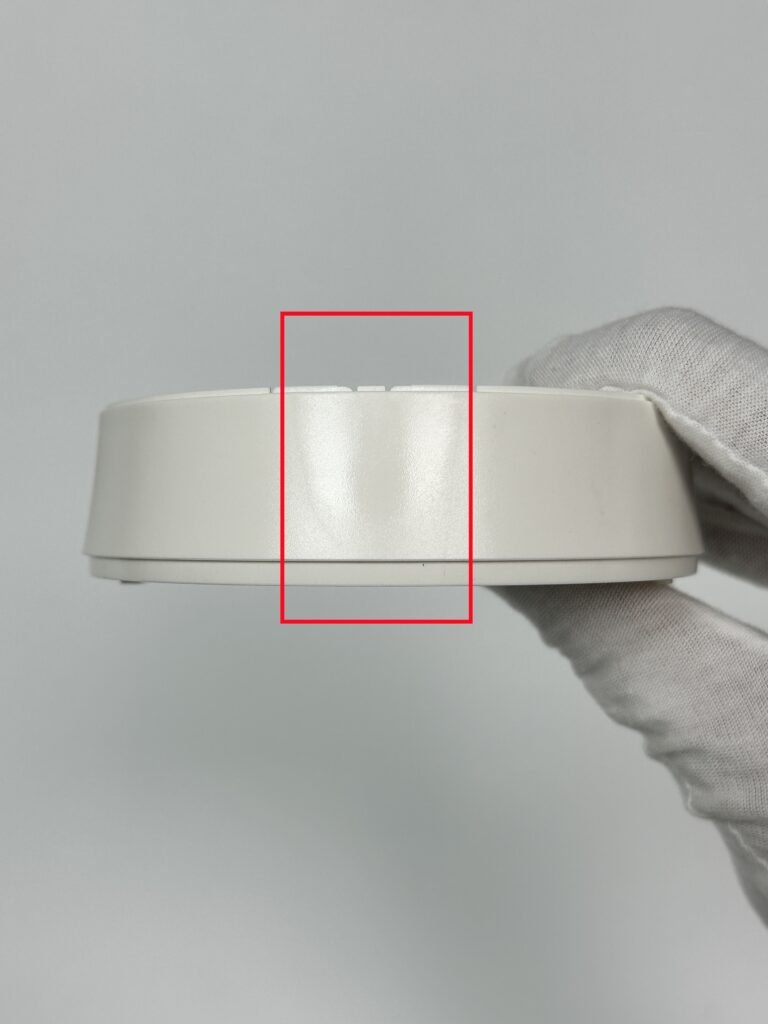
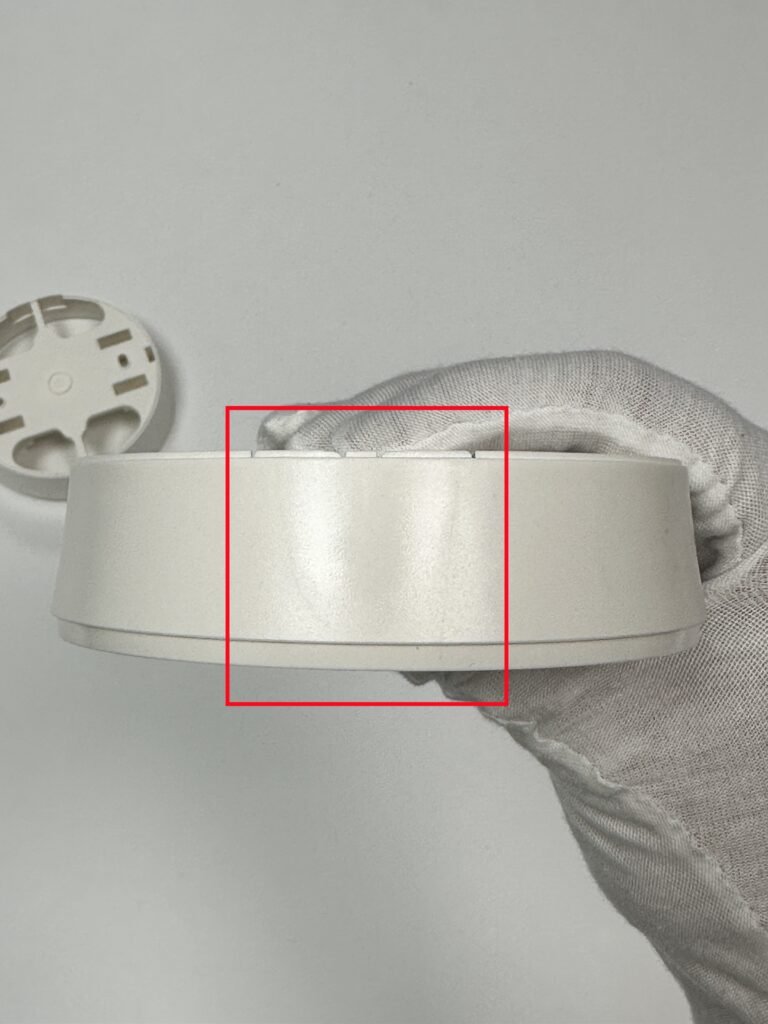
Causes of weld lines and our solutions
At Ruicheng, through years of extensive injection molding experience and numerous experiments, we have thoroughly researched the causes of weld lines. Below is a detailed account of how we identified these causes in an actual project:
Project Background: In a critical medical device project, our customer had extremely high requirements for the appearance and structural integrity of the parts. During production, the customer reported visible weld lines on the product surface, affecting both aesthetics and performance.
System Analysis and Experiments: We first conducted a comprehensive system analysis of the production process for this project, meticulously recording and observing each step. We assembled a dedicated team to deeply investigate the weld line issue.
Material Flow Front Convergence: Using high-precision imaging equipment and flow analysis software, we observed the flow paths of the molten plastic within the mold. When multiple flow fronts converged, we found they did not fully merge, resulting in weld lines. Through simulations and experiments, we identified the specific locations and conditions of these flow front convergences.
Improper Temperature Control: With the aid of temperature sensors and thermal imaging technology, we monitored the temperature distribution of the molten plastic during the injection process. Our experiments showed that low molten plastic temperature led to insufficient flowability, preventing full merging at the convergence points and forming weld lines. We conducted a series of tests to adjust temperature parameters, verifying this issue and determining the optimal temperature settings.
Improper Injection Speed and Pressure Settings: We conducted multiple experiments by adjusting the speed and pressure settings of the injection molding machine. The results indicated that low injection speed and pressure caused the molten plastic to flow more slowly in the mold, preventing full merging at the convergence points and forming weld lines. By optimizing these parameters, we significantly reduced the occurrence of weld lines.
Mold Design Deficiencies: We performed a detailed analysis of the mold design, focusing on the layout of cooling channels and venting. We found that certain areas with poor design led to uneven cooling and air entrapment. Collaborating with mold designers, we redesigned these areas, added vents, and optimized the cooling channel layout.
Air Entrapment: During our experiments, we discovered that air trapped within the molten plastic was another major cause of weld lines. By improving the mold's venting design and adding vent channels, we greatly reduced air entrapment, significantly lowering the incidence of weld lines.
Results Verification: Through these systematic studies and experimental adjustments, we successfully resolved the weld line issue in the medical device project. The weld lines on the product surface were significantly reduced, meeting the customer's high standards. The customer was highly satisfied with our solution and further strengthened their cooperation with us.
Through these detailed studies and the experience gained from actual projects, we have deeply understood the root causes of weld lines and developed effective solutions. Leveraging this knowledge and technology, Ruicheng can produce high-quality, weld line-free plastic parts that meet our customers' high standards.
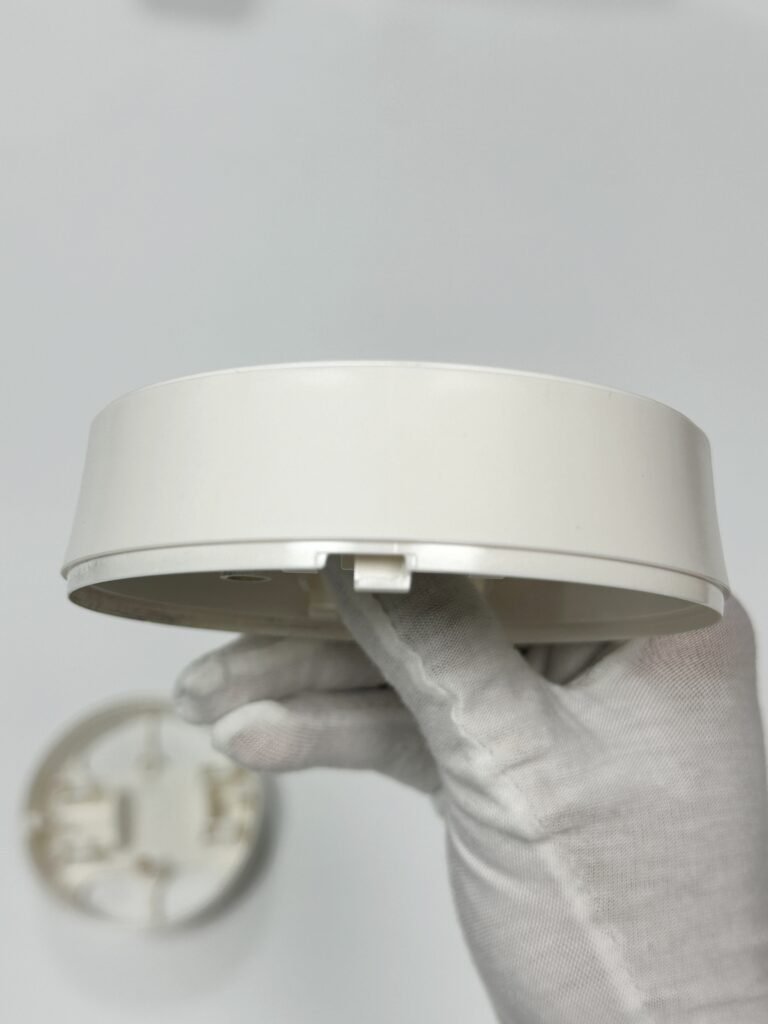
Our Experienced & Professional Solutions
In the injection molding process, weld lines are linear defects formed when two or more fronts of molten plastic meet in the mold cavity without fully fusing. These defects not only affect the appearance of the product but also reduce its mechanical properties. Ruicheng has extensive experience and special solutions for addressing weld line issues. Here are our methods and technologies:
1.Increasing Material Temperature:
- Optimizing the Heating System: We optimize the heating system of the injection molding machine to ensure that the plastic reaches the proper melting temperature before entering the mold. By increasing the material temperature, the flow fronts can fully fuse in the mold, reducing the formation of weld lines.
- Uniform Temperature Control: During the injection process, we maintain uniform mold temperature to avoid localized low temperatures that can lead to weld line issues.
2.Optimizing Mold Design:
- Redesigning Gate Position: Using flow analysis software, we simulate the flow paths of the plastic and redesign the gate positions and runner layouts to reduce the flow distance of the molten plastic in the mold. This allows the flow fronts to merge at higher temperatures, decreasing the likelihood of weld line formation.
- Adding Venting Ports: We add venting ports at critical positions in the mold to ensure that air can be expelled smoothly, reducing the obstruction of molten plastic flow by air and improving material fusion.
- Adding Cold Slug Well: By designing a specialized cold slug well in the mold, it can capture and discharge solidified cold material due to cooling, preventing it from entering the product area within the mold cavity. This avoids the cold material from merging with the flow fronts of the molten plastic, reducing the formation of weld lines, and significantly improving the product's appearance quality and mechanical performance.
3.Adjusting Injection Parameters:
- Increasing Injection Speed and Pressure: Through experiments and testing, we find the optimal injection speed and pressure settings. Increasing the injection speed and pressure allows the molten plastic to fill the mold more quickly and evenly, reducing the formation of weld lines.
- Optimizing Packing and Cooling Time: We adjust the packing and cooling time to ensure that the plastic maintains appropriate pressure and temperature during solidification, promoting complete fusion of the flow fronts.
- Increasing Injection Temperature:Increasing the injection temperature can effectively solve weld line issues. By raising the temperature of the molten plastic, its flowability and fusion within the mold are improved, ensuring that the flow fronts fully merge when they meet, thereby reducing the formation of weld lines.
4. Selecting Suitable Materials:
- High-Flow Materials: Choosing plastic materials with high flowability can enhance the filling capability of the molten plastic, making it easier for the flow fronts to merge in the mold, thereby reducing weld lines.
- Use of Additives: Using specific additives, such as flow modifiers, can improve the flowability and fusion performance of the material, further reducing the formation of weld lines.
5.Regular Maintenance and Calibration of Equipment:
- Equipment Maintenance: We regularly conduct comprehensive maintenance and calibration of injection molding machines and molds to ensure that the equipment is in optimal working condition, preventing weld line issues caused by equipment failures.
- Quality Monitoring: We establish a strict quality monitoring system to continuously monitor key parameters during the injection process, allowing us to detect and adjust any potential issues that could lead to weld lines.
Result Validation
Through these comprehensive measures, we have successfully resolved weld line issues in multiple projects. For example, in an electronic product housing production project, we applied the above methods, resulting in a smooth surface with no visible weld lines on the produced housing, meeting the client's high standards for appearance and mechanical performance. The client was highly satisfied with our solutions, which not only improved product quality but also significantly reduced scrap rates and rework costs.