Problem Explanation
Warping of injection-molded parts typically occurs due to uneven shrinkage of the material during the cooling process or improper mold design. This deformation can affect the dimensional accuracy and appearance of the product, especially in applications requiring high precision, such as electronic components or automotive parts.
Case Background
An automotive parts manufacturer commissioned us to produce a batch of plastic panels for door interiors. Upon receiving the first batch of samples, the client noticed that some panels exhibited significant warping after installation, preventing them from fitting perfectly with the door.
Problem Analysis
After analysis by our technical team, it was determined that the primary cause of the warping was uneven cooling during the injection molding process. Due to significant variations in the thickness of the panels across different areas, thicker sections cooled more slowly, leading to uneven shrinkage and resulting in warping.
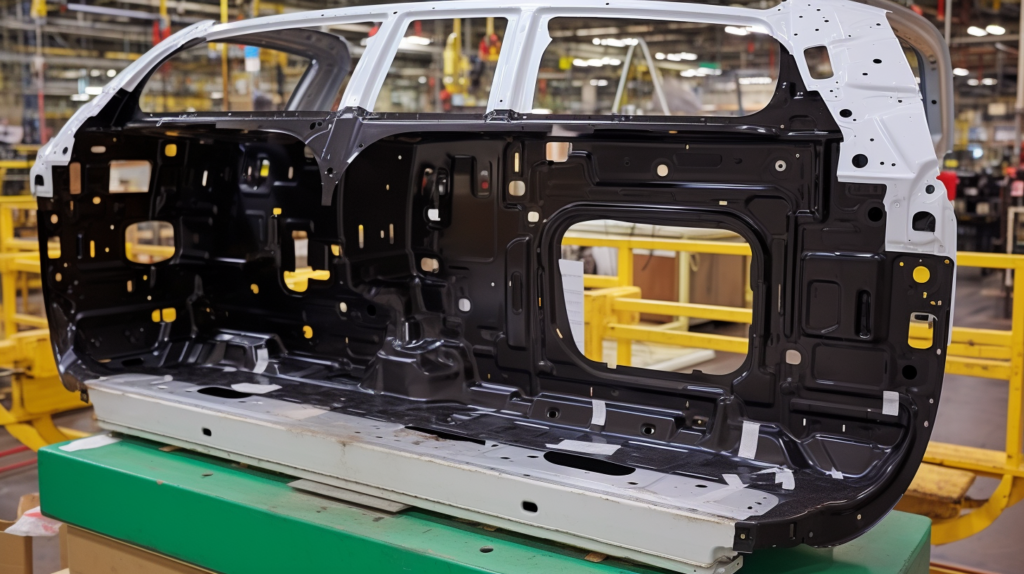
Solution
We implemented the following measures to address the issue:
- Optimized Mold Design: Added additional cooling channels in the mold to ensure more uniform cooling across all areas.
- Adjusted Injection Molding Parameters: Modified the injection speed, pressure, and cooling time to further reduce warping.
- Material Selection: Switched to a plastic material with a lower shrinkage rate to minimize differences in shrinkage during cooling.
Result
After these adjustments, the newly produced plastic panels no longer exhibited warping after installation and fully met the client's dimensional and aesthetic requirements. The client was highly satisfied with our solution and decided to continue collaborating with us for future production.
Through this case, we demonstrated how to address warping in injection-molded parts through technical measures, ensuring product quality and customer satisfaction.