What are Air Bubbles?
Air bubble issues refer to the presence of gas pockets inside or on the surface of plastic parts during the injection molding process. These bubbles are typically formed when volatile substances or moisture in the material vaporize during heating. These air bubbles not only affect the appearance of the product but also negatively impact its mechanical properties and structural integrity. Air bubbles can cause visible defects on the product surface, affecting its aesthetics and market acceptance. For products with high appearance requirements, air bubbles may lead to the product being directly classified as defective.
Furthermore, the presence of air bubbles weakens the continuity and uniformity of the material, leading to a decrease in the product's strength, toughness, and durability, making it prone to cracking or breaking during use. Air bubbles compromise the internal structure of the product, reducing overall stability and reliability. In applications requiring high precision and high strength, air bubbles can cause the product to malfunction or fail prematurely. For certain functional components, air bubbles can even affect performance; for example, bubbles in sealing parts can lead to seal failure, and bubbles in electronic components can impact electrical performance.
Air bubble issues also increase scrap rates and rework costs, reducing production efficiency. Manufacturers need to invest additional resources to inspect and repair these defective products, increasing production costs. Moreover, air bubble issues can lead to customer dissatisfaction with product quality, affecting customer satisfaction and the company's reputation.
Causes of Air Bubble Issues in Injection Molding
In the injection molding process, air bubble issues are often caused by multiple factors:
Material Issues: Moisture or volatile substances in the plastic material vaporize during heating, leading to the formation of air bubbles. If the material is not adequately dried, residual moisture can exacerbate this problem.
Mold Design: Improper mold design, such as insufficient venting systems, can prevent air from being expelled smoothly, causing air to become trapped in the mold cavity and form bubbles.
Processing Parameters: Injection speed that is too fast or pressure that is too high can prevent air from being expelled smoothly, increasing the risk of air bubble formation. Incorrect injection temperature settings can also affect the flowability of the plastic, making it easier for bubbles to form.
Equipment Issues: Mechanical failures or inadequate maintenance of the injection molding machine can also lead to air bubble problems. For example, worn screws or faulty heating systems can introduce air into the plastic as it is injected into the mold, forming bubbles.
The combined effect of these factors results in the formation of air bubbles during the injection molding process.
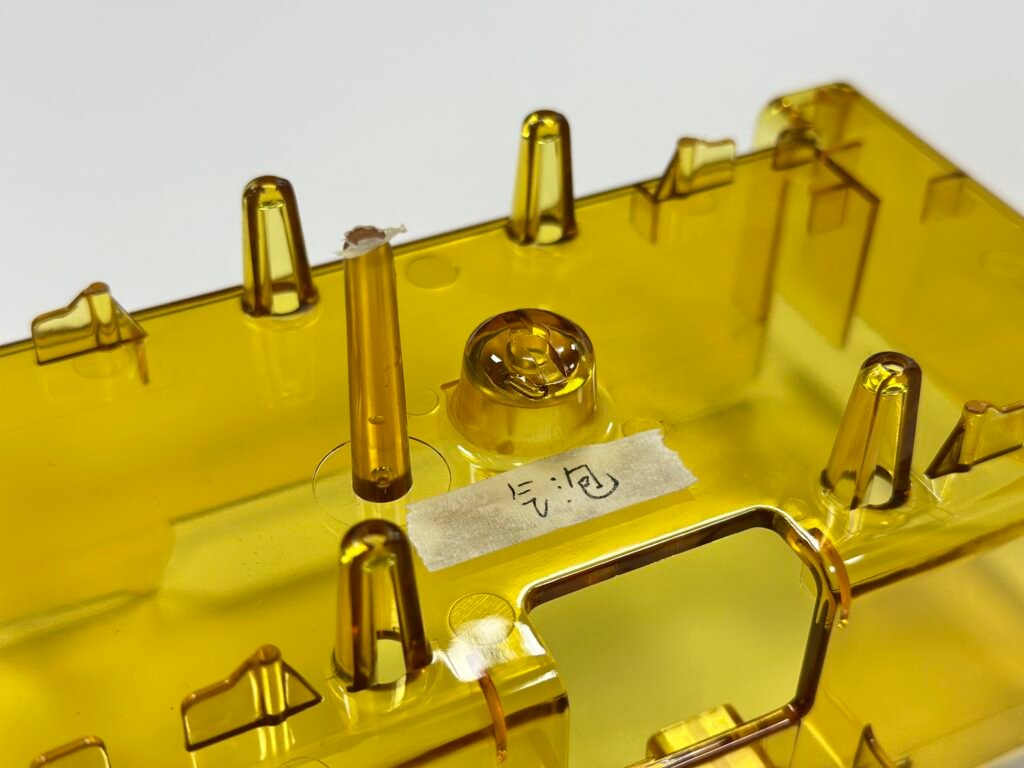
Methods to Solve Air Bubble Issues
At Ruicheng, we have extensive experience in injection molding and a comprehensive set of professional solutions to address air bubble issues. Here’s how we systematically solve this common problem:
First, we start with material handling. To prevent moisture and volatile substances in the material from vaporizing during heating, we use efficient drying equipment to thoroughly dry all plastic materials. This ensures that the material has optimal flow properties during the injection molding process and reduces the formation of air bubbles.
Next, we optimize mold design. Using advanced design software for mold flow analysis, we ensure that the mold's venting system is well-designed. By adding more vents and optimizing vent channels, we can effectively expel air from the mold cavity, preventing the formation of bubbles.
In terms of processing parameter settings, our engineers precisely adjust injection speed, pressure, and temperature based on the specific material and product requirements. Through a series of experiments and tests, we find the best parameter combinations to ensure the molten plastic fills the mold cavity smoothly without forming bubbles.
Additionally, we regularly maintain and calibrate our injection molding equipment. Ensuring that screws, heating systems, and other critical components are in optimal working condition helps prevent air bubbles caused by equipment malfunctions. Our technical team has extensive experience in equipment maintenance, allowing us to quickly identify and resolve potential issues, ensuring a smooth production process.
Through these comprehensive measures, Ruicheng effectively solves air bubble issues while ensuring high product quality and reliability. Our customers are highly satisfied with our solutions and continue to choose us as their long-term partner.
This systematic, professional, and experienced approach keeps Ruicheng at the forefront of the injection molding industry, meeting the stringent demands of customers for high-quality products.