What is Short Shot?
Short Shot refers to a common defect in the injection molding process where the molten plastic fails to completely fill the mold cavity, resulting in an incomplete part or missing sections of material. This issue typically manifests in insufficient material at the edges, corners, or complex structures of the part, leading to an incomplete product. Short shots not only affect the appearance of the product but also impair its function and performance, preventing it from meeting design and usage requirements.
The Seriousness of Short Shot
Short Shot is a severe defect in the injection molding process that can have multiple negative impacts on product quality and production efficiency:
Product Quality:
Short shot leads to incomplete products, with insufficient material at the edges, corners, or complex structures, directly affecting the appearance and function of the product. This incompleteness means the product cannot meet design and usage requirements, potentially reducing its market competitiveness.
Mechanical Performance:
Insufficient material in areas affected by short shot significantly reduces the part's mechanical properties, including strength, durability, and toughness. The affected parts are more likely to break, deform, or fail during actual use, impacting the overall reliability and lifespan of the product.
Structural Integrity:
Material deficiencies caused by short shot compromise the structural integrity of the part, making it more prone to damage during assembly and operation. This is especially serious for products that require precise assembly and high-strength use, such as automotive components and electronic device housings.
Production Efficiency:
Short shot issues increase scrap rates and rework costs, leading to decreased production efficiency. Manufacturers need to invest additional time and resources to repair or remanufacture defective parts, extending production cycles and increasing manufacturing costs.
Customer Satisfaction:
Short shots affect the final quality of the product, leading to increased customer complaints and returns, damaging the company's reputation and customer satisfaction. Persistent short shot issues can cause customers to lose confidence in the supplier, affecting business relationships and market share.
Safety Risks:
In critical applications such as medical devices and aerospace parts, short shots pose serious safety risks. The reduction in product performance and reliability can lead to equipment failure, potentially endangering personal safety.
Due to these reasons, short shot issues in the injection molding process must be given high attention.
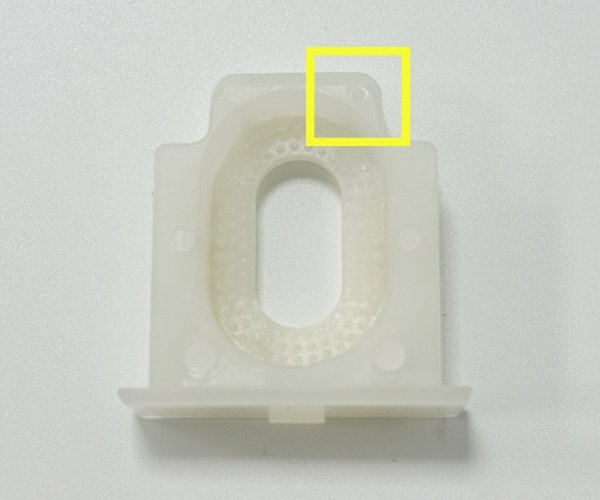
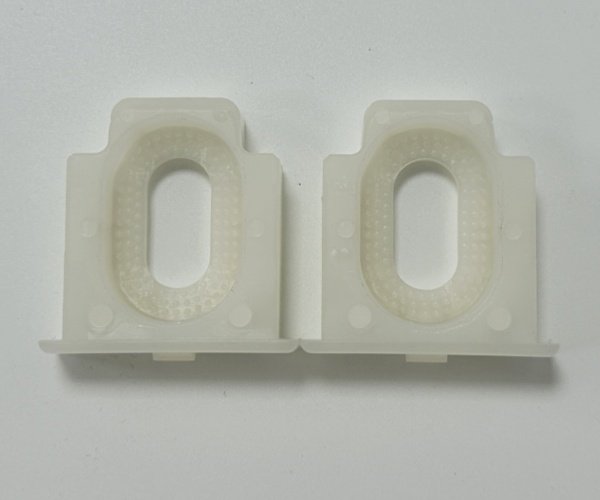
Challenges encountered in the project and solutions
In the production of mobile phone cases, we encountered a series of problems caused by short shots. Due to the complexity and precision required in mobile phone case design, certain areas experienced insufficient material filling, especially at the edges and corners. Specific problems included:
Surface Defects:
The surface of the mobile phone cases showed obvious short shot marks, leading to an unattractive appearance. These surface defects severely impacted the overall look and user experience of the product.
Structural Strength Insufficiency:
Areas with short shots had insufficient material, resulting in decreased structural strength of the mobile phone case. In actual use, the case was prone to cracking or deforming when subjected to external forces, affecting durability and safety.
Assembly Issues:
Short shots also affected the precision assembly of the mobile phone cases, leading to poor fitting with internal components. This caused gaps or looseness during assembly, affecting the overall quality of the device.
Solutions
To address these short shot issues, we implemented the following effective measures:
Optimizing Mold Design:
We redesigned the molds, optimizing the gate locations and runner layouts to ensure smooth flow and even filling of the mold cavity by the molten plastic. Using simulation software, we analyzed the plastic flow paths to avoid flow front collisions and separations, enhancing the filling effect.
Adjusting Injection Parameters:
We finely adjusted the injection speed, pressure, and temperature settings of the injection molding machine. By increasing injection pressure and speed, we ensured that the molten plastic quickly filled the mold cavity. Additionally, we optimized mold temperature and cooling time to prevent premature cooling during the filling process.
Using High-Quality Materials:
To improve the flowability and filling capability of the plastic, we selected higher quality materials with better flow characteristics. These materials were pretreated and dried to ensure optimal performance during injection molding, reducing the occurrence of short shots.
Enhancing Venting:
We added more venting points in the mold design to ensure that air in the mold cavity could be effectively expelled, avoiding the formation of bubbles and gas traps. Improving the venting system effectively prevented short shot issues.
Strict Quality Control:
We implemented strict quality control measures throughout the production process, from raw material inspection to final product testing. Each stage underwent rigorous checks and tests to ensure every mobile phone case met high-quality standards without short shots or other defects.
Through these systematic solutions, we successfully resolved the short shot issues in mobile phone case production, significantly improving product quality and customer satisfaction. Customers highly recognized our solutions and strengthened their cooperation with us.