What are Gas Traps
Gas traps refer to the phenomenon in the injection molding process where air or other gases are trapped inside the mold cavity and cannot be effectively expelled. These gases are encased within the plastic, forming bubbles or other defects that affect the appearance and quality of the product. Gas trap issues are significant in the injection molding process because they directly impact the quality and performance of the products. Gas traps can cause bubbles, burn marks, or incomplete filling on the product surface, severely affecting the product's aesthetics and structural integrity. Furthermore, gas traps weaken the mechanical properties of the material, making the product more prone to cracking or failure during actual use. Therefore, addressing gas trap issues is crucial to ensuring the high quality and reliability of injection-molded products.
Common Causes of Gas Traps
In the injection molding process, gas trap issues are often caused by the following factors:
Improper Mold Design:
Insufficient venting system in the mold prevents air from being expelled smoothly, leading to air being trapped inside the mold cavity.
Incorrect placement of gates and runner designs hinders the flow of plastic, making it difficult for gases to escape.
Incorrect Injection Parameters:
If the injection speed is too fast, the molten plastic fills the mold quickly, leaving insufficient time for the air to be expelled.
High injection pressure can also trap air within the plastic, forming bubbles.
Material Issues:
Volatile substances or moisture present in the plastic material can vaporize during heating, causing gases to be trapped inside the mold.
Uneven Mold Cooling:
Poorly designed mold cooling systems can lead to uneven internal temperatures in the mold, making it difficult for gases to be expelled smoothly.
Injection Machine Equipment Problems:
Mechanical failures or inadequate maintenance of the injection molding machine, such as worn screws or unstable heating systems, can introduce air into the plastic and trap it.
The combined effects of these factors lead to gas trap issues during the injection molding process, affecting the quality and performance of the products.
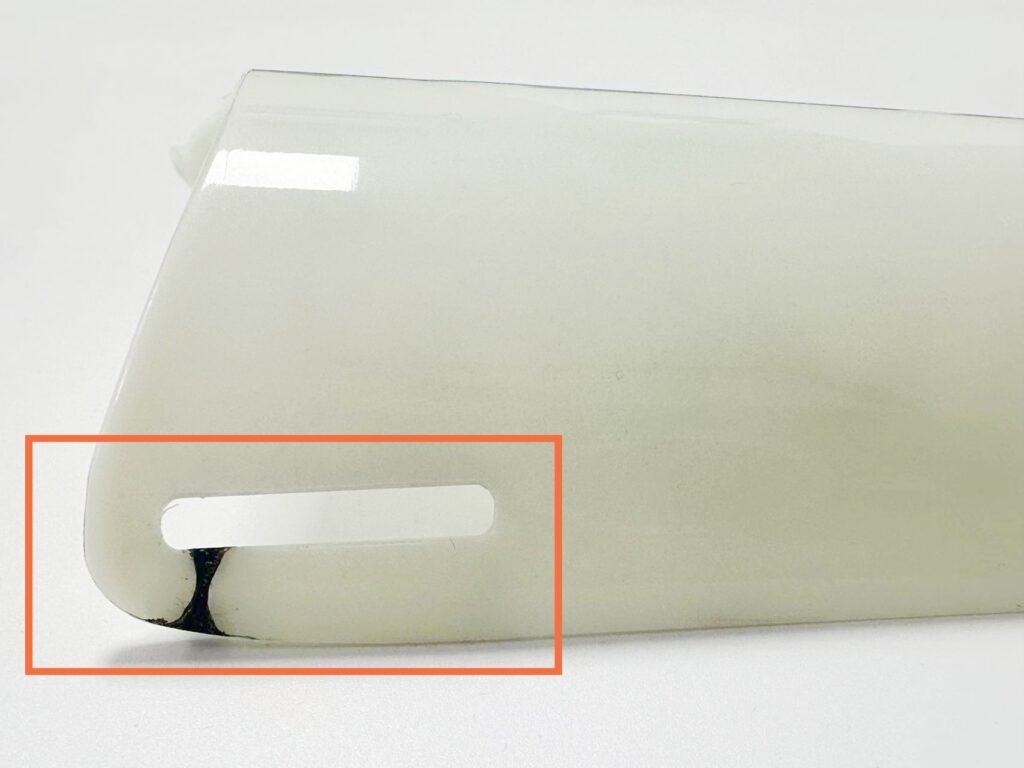
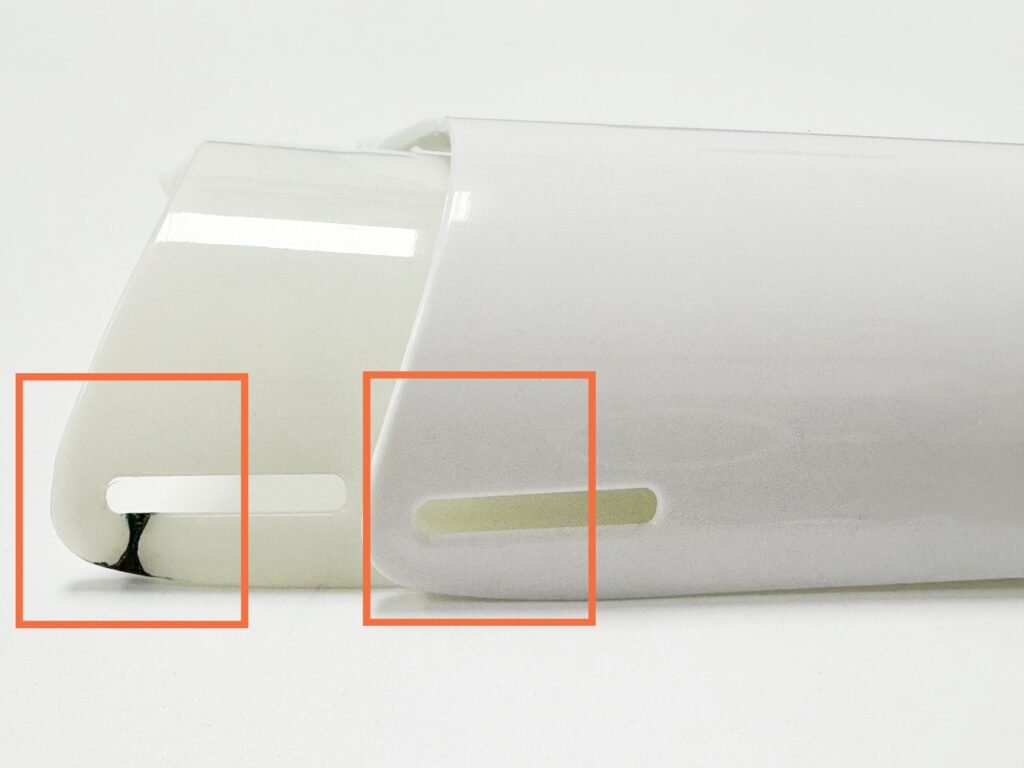
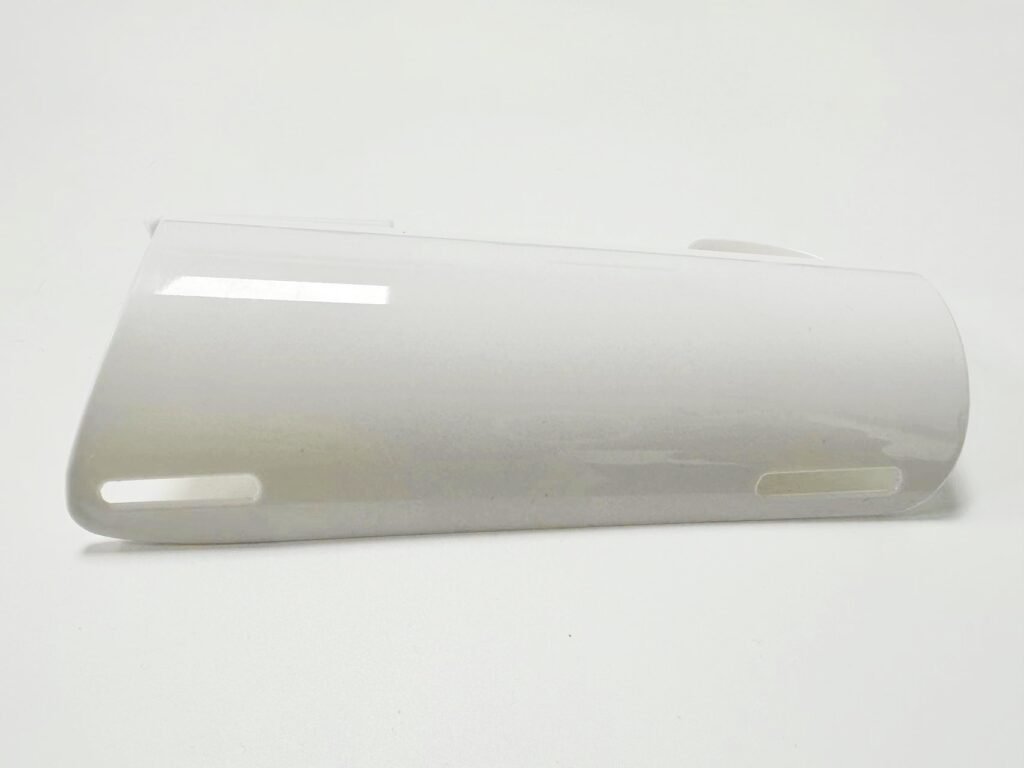
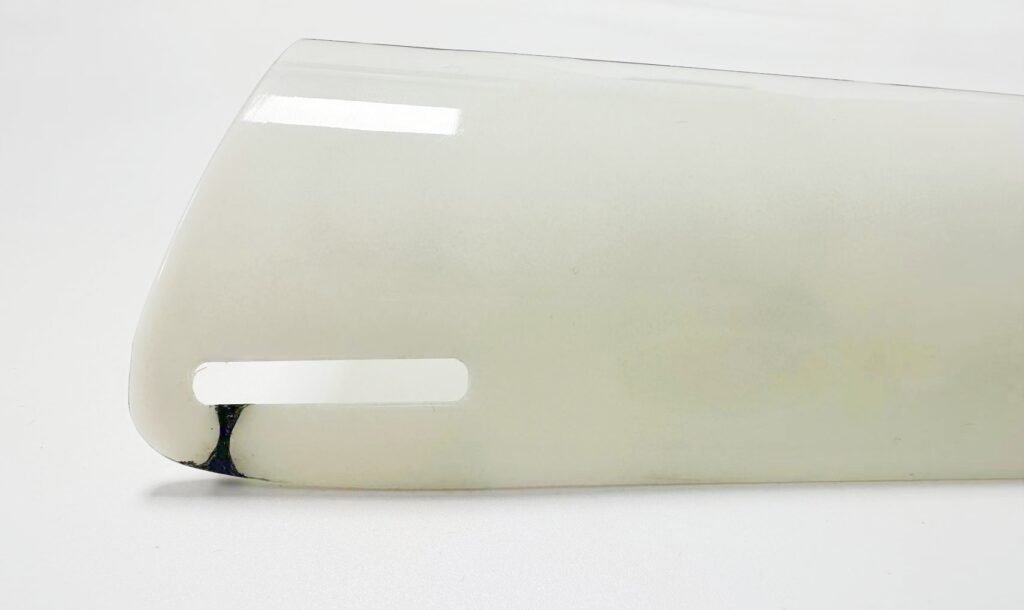
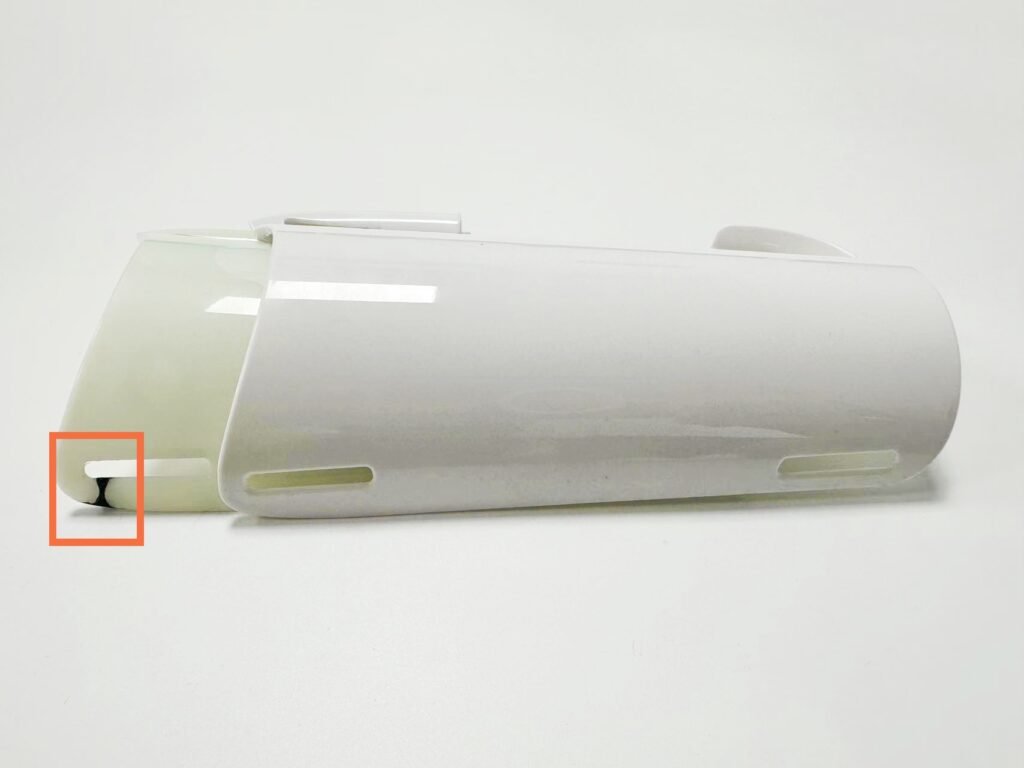
Case Study: Solving Gas Trap Issues in Automotive Dashboard Production
Project Background
During the production of automotive dashboards, we encountered gas trap issues, leading to surface bubbles and burn marks. These defects severely affected the appearance and performance of the products. Given the high standards for the appearance and structural integrity of automotive dashboards, this issue needed urgent resolution.
Implementation of Solutions
Optimizing Mold Design:
We redesigned the mold’s venting system, adding more vents and optimizing vent channel layouts to ensure that air could be expelled smoothly from the mold cavity.
Adjusted the placement of gates and runner designs to ensure the molten plastic could flow smoothly during mold filling without trapping air.
Adjusting Injection Parameters:
Through experiments and testing, we identified the optimal injection speed and pressure settings to ensure the molten plastic could fill the mold smoothly while giving the air enough time to be expelled.
Optimized injection temperature settings to enhance plastic flowability, reducing the risk of bubble formation.
Improving Material Handling:
Utilized efficient drying equipment to thoroughly dry the plastic materials, removing moisture and volatile substances to prevent vaporization and bubble formation during heating.
Equipment Maintenance:
Conducted comprehensive maintenance of the injection molding machines, ensuring that screws, heating systems, and other critical components were in optimal working condition to avoid air being introduced due to equipment failures.
Results Verification: Through these comprehensive measures, the gas trap issues in the automotive dashboards were significantly improved. The produced dashboards had smooth surfaces, free of bubbles and burn marks, with complete structural integrity and excellent mechanical performance.