The Journey of Blow Molding
Innovative Blow Molding Technology Redefining Manufacturing Possibilities
Descriptions
We specialize in blow molding with ±0.1mm wall thickness control and multi-layer barrier technology.
Our automated lines produce 500ml bottles in 5 seconds with >99.5% quality rate.
Trusted by chemical and FMCG brands for complex container solutions.
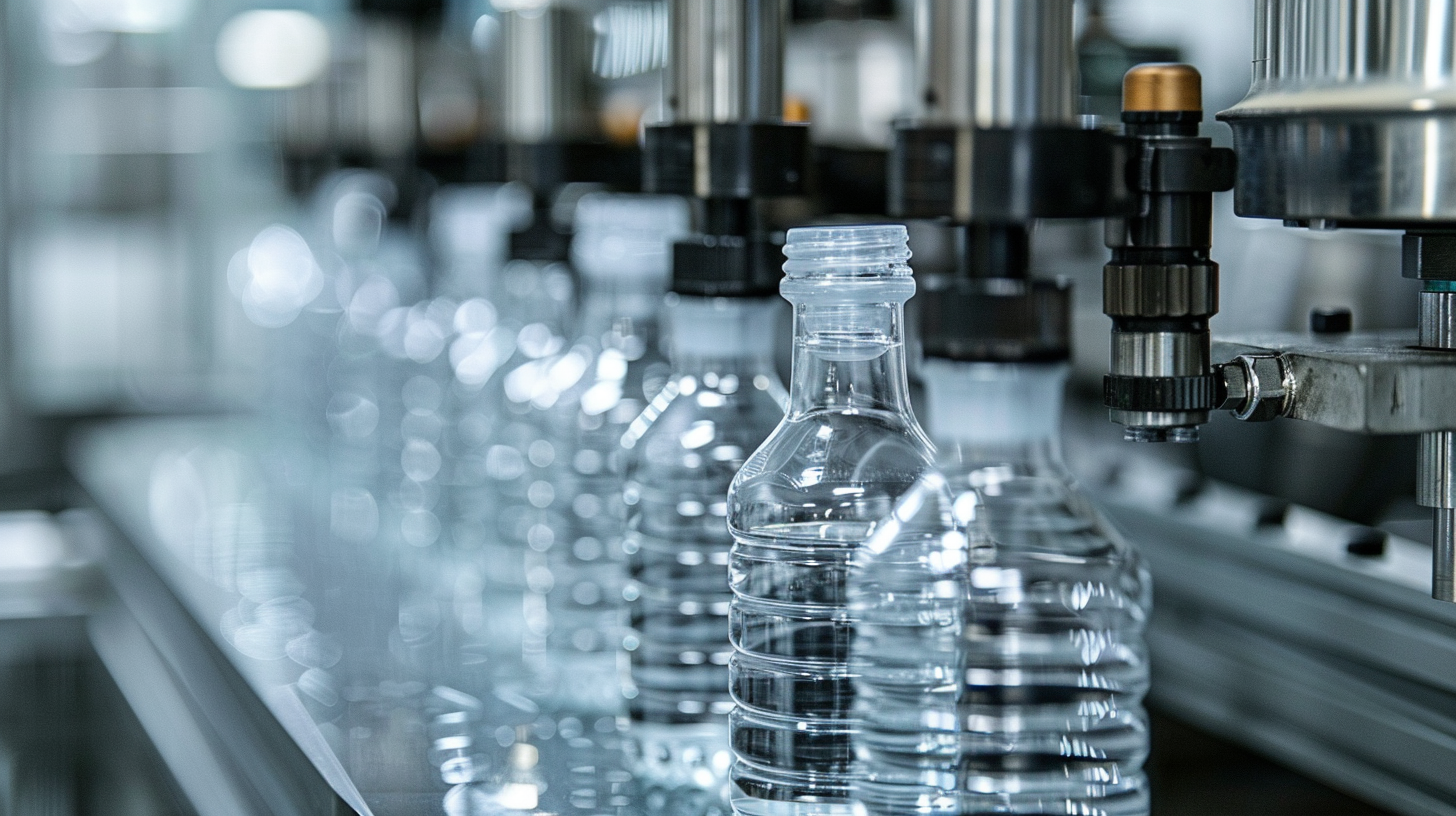
Key Points
- Efficient Production: Blow molding allows for high-speed production of hollow plastic parts, making it ideal for large-scale manufacturing.
- Versatile Applications: Widely used for creating containers, bottles, and other hollow parts across various industries such as food and beverage, pharmaceuticals, and automotive.
- Material Flexibility: Suitable for a variety of thermoplastics including PET, HDPE, and PVC, allowing for diverse product properties.
- Complex Shapes: Capable of producing complex and intricate shapes with varying wall thicknesses, offering design flexibility and innovation in product development.
- Cost-Effective: The process is economical for mass production, reducing material waste and production costs.
- Consistency and Quality: Produces uniform wall thickness and strong, durable products with excellent surface finish.
Why choose us as your partner
Advanced Technology: Utilizing state-of-the-art machinery and techniques to ensure precision and efficiency in every production step.
Experienced Team: A skilled and dedicated team with over 20 years of experience in the plastic injection molding industry.
Quality Assurance: Stringent quality control measures in place to guarantee that every product meets the highest standards.
Customized Solutions: Tailored services to meet specific client needs, from initial design to final production.
Timely Delivery: Efficient production processes and logistics ensure on-time delivery for every order.
Sustainability Focus: Committed to environmentally responsible practices, minimizing waste and maximizing efficiency.
Get In Touch
Get in touch and let us know how we can help.
No.50, Liheng Industrial Zone, Xinglin West Road, Jimei District, Xiamen, China
marketing@chinaruicheng.com
WhatAPP : +8615159297535